LAWRENCE – One word best defines how Megan Landes-Murphy and her husband Tom Murphy met, made career choices and launched a unique-to-Nebraska business.
Sheep. Neither spent much time around the animals while growing up in northwest Wisconsin and the Omaha area, respectively.
Now, they have sheep, a few chickens and two Great Pyrenees dogs named Milo and Birdie on their 12-acre ranch east of the small south-central Nebraska town of Lawrence.
Two years ago, Landes-Murphy launched Kestrel Ridge Pellet Co., a garage-based business that processes wool into natural fertilizer.
It’s a small solution to a big problem. Most Nebraska sheep have low-grade wool – not the fine wool used in high-quality yarns and fabrics – because they are bred for their meat.
Even if a low-grade wool buyer is found, the price paid might not cover shearing costs, Landes-Murphy said, so many sheep owners bury or burn that wool. She and her husband have used such fleeces for erosion protection in their pasture.
Nebraska had 76,000 sheep and lambs on Jan. 1, according to the U.S. Department of Agriculture. Shorn wool production totaled 245,000 pounds in 2023.
“There’s a lot of wool going into landfills right now,” said Dan Stehlik, president of the Nebraska Sheep and Goat Producers Association.
The journey that led Landes-Murphy to form Kestrel Ridge Pellet Co. started with a simple question: What to do with all the lowgrade wool?
Kestrel Ridge Ranch is home to 20 Shropshire ewes and five rams. Like most sheep in Nebraska, the couple’s herd are all meat producers and breeding stock.
“They’re kinda short and stout,” Landes-Murphy said.
Connie Moore, Chadron, the sheep association’s secretary, estimates that fewer than 20 percent of Nebraska sheep are fine wool breeds, like her 130 Rambouillets.
“Really, we don’t have a lot of places to take our wool,” she said.
She takes hers to a northwest South Dakota buyer located nearly 200 miles from Chadron.
Landes-Murphy’s online searches for alternative low-grade wool markets led her to University of Vermont research on wool pellets.
Field trials at a few Vermont fruit and vegetable farms showed that wool pellets can absorb, hold and release water and nutrients over time, fertilizing crops with “generous” nitrogen and then safely incorporating into the soil.
A report from another trial, with spinach and tomatoes, says, “Overall, wool pellets performed very similarly to commercial organic fertilizer . . . and could be a promising alternative that may open opportunities for greater integration of plant and animal systems on diversified farms.”
Landes-Murphy started Kestrel Ridge Pellet Co. after spring shearing in 2022. Her twostep processing equipment is a wool shredder made by an Indiana manufacturer and a pellet mill, like ones used for wood pellets.
She knew her pellets wouldn’t be economically feasible for large-scale fruit and vegetable growers, who have access to less expensive fertilizers.
“I would describe my target as backyard gardeners who have raised beds or potted plants, including flowers,” Landes-Murphy said.
Why sheep?
Megan Landes-Murphy and Tom Murphy didn’t grow up around sheep.
Landes-Murphy, the daughter of a carpenter and a music teacher, grew up 20 miles outside of Rice Lake, Wisconsin, a rural upbringing but not a farm one.
Her bachelor’s degree from the University of Wisconsin at Madison was in wildlife ecology.
Murphy, who graduated from Mount Michael High School in Elkhorn, earned bachelor’s and master’s degrees at the University of Nebraska-Lincoln. He arrived intending to be a veterinarian, but switched to genetics for his master’s degree. Then he headed to Wisconsin-Madison to teach sheep-related classes and earn his Ph.D.
“My best friend was taking his (Tom’s) sheep production class and one time I went with her to the lambing barn. I was sold on lambs,” Landes-Murphy said.
And, apparently, also on Tom. They were married Aug. 25, 2018.
They spent 2 ½ years in Bozeman,where Murphy was a Montana State University professor of sheep production. It was an expensive place to live, let alone buy land.
So they applied for jobs at the USDA Meat Animal Research Center near Clay Center, where Murphy still works as a research geneticist specializing in sheep. Landes-Murphy worked there for three years as a lab technician. They bought their Lawrence ranch property in 2021.
They’re still renovating the 100-year-old farmhouse, and have a big red barn,four other outbuildings, a pasture divided by electric fencing into eight rotational grazing areas, and a corral and sheep shed on a hill above the barn.
The sheep graze from spring through fall, and are fed purchased grass or prairie hay and protein supplement over the winter. Lambs are born in late April and early May, a month after the flock is sheared by a Lawrence area crew who schedule shearing around full-time jobs.
Landes-Murphy processes 10,000 pounds of wool into pellets a year, roughly 250 pounds from her flock and the rest from the shearers who have customers within 200 miles of Lawrence. The wool needs to be used within a year, otherwise it becomes too dry and won’t make good pellets.
The low-grade wool would fetch pennies per pound on the market. Landes-Murphy said the shearers typically pay a little more and then she buys what she needs for 15-20 cents a pound.
“Some just give it to the shearers for free,” she added.
Testing pellets
It cost around $14,000 to get the wool pellet business up and running, Landes-Murphy estimated, including shredding and pellet machines, packaging and other expenses. Samples from each batch of wool are tested at an agriculture lab to confirm the levels of nitrogen and other nutrients.
Eventually it came time to see how the pellets performed.
In 2022, Landes-Murphy contacted Katie Jantzen, owner of West End Farm near Plymouth, about doing wool pellet trials.
Jantzen grows 50 plant varieties – vegetables, melons, berries, herbs and flowers.
Her 2023 trials were on three varieties of broccoli, three varieties of cauliflower and one type of potato. The broccoli did better with wool pellets. The potatoes did, too, with the test bed producing more than the control bed, 212 pounds to 178 pounds. The cauliflower performed equally well with wool pellets and standard fertilizer.
Jantzen was impressed with the results, but she also determined that wool pellets wouldn’t be cost effective for her large, halfacre business.
An entrepreneur
Pellet processing, marketing and shipping go smoother for Landes-Murphy now. Her krpelletco.com website has packaged pellets for sale in four sizes, from $15 for a 1-pound bag to $120 for 20 pounds.Customers also can get “bring-your-own bag” bulk amounts.
She promotes the business through her website, on social media and at events such as the Nebraska State Arboretum plant sale in Lincoln. Still, spreading the word remains difficult “because not a lot of people have heard of wool pellets.”
Sheep association leaders Moore and Stehlik said Landes-Murphy is the only Nebraskan they know of who makes wool pellets.
“It’s really wonderful to try to create or explore a value-added purpose for wool in the Midwest, where we don’t have many of the fine wools,” Stehlik said, adding that the challenges ahead are to have larger-scale processing and use of wool pellets.
At this point, Landes-Murphy is producing about as many pellets as she can without getting a bigger pellet mill. Eventually, she’d like to scale up.
For now, Landes-Murphy is still getting used to being described as an entrepreneur.
“It’s been a slow process seeing myself in that light,” Landes-Murphy said, describing herself as a lifelong learner. “I thought mostly about having jobs working for someone else, but I like this.”
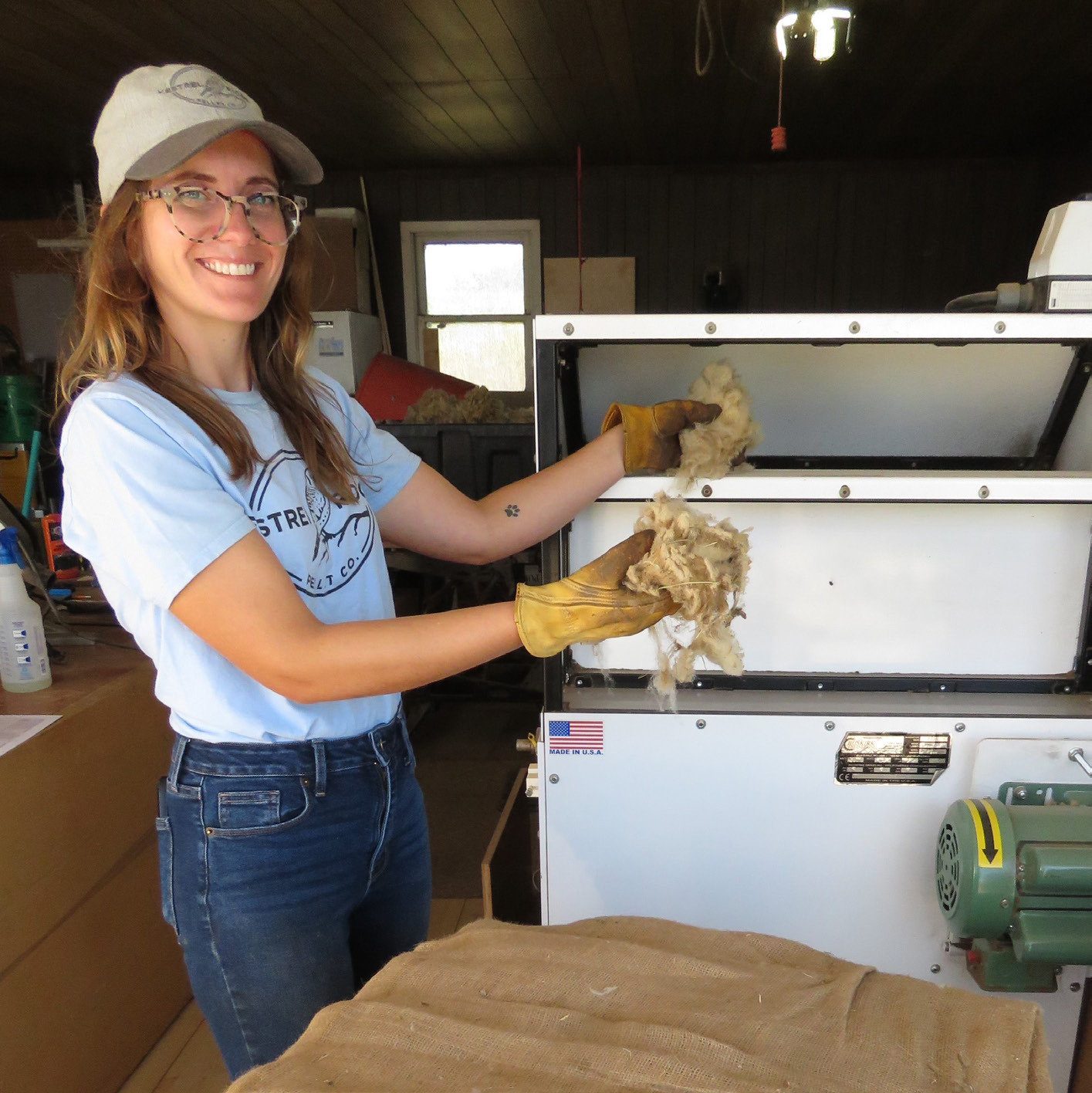
The two-step process to make Kestral Ridge Pellet Co. wool pellets starts with a shredder Megan Landes-Murphy ordered from an Indiana manufacturer. Fleeces are cut into smaller pieces before being put into the pellet mill. At far left, Tom Murphy herds some of his sheep on a pasture hill near a corral and sheep shed. The Elkhorn native didn’t work with sheep until college, and now is a research geneticist specializing in sheep at Clay Center’s USDA Meat Animal Research Center. Photo by Lori Potter |for the Flatwater Free Press
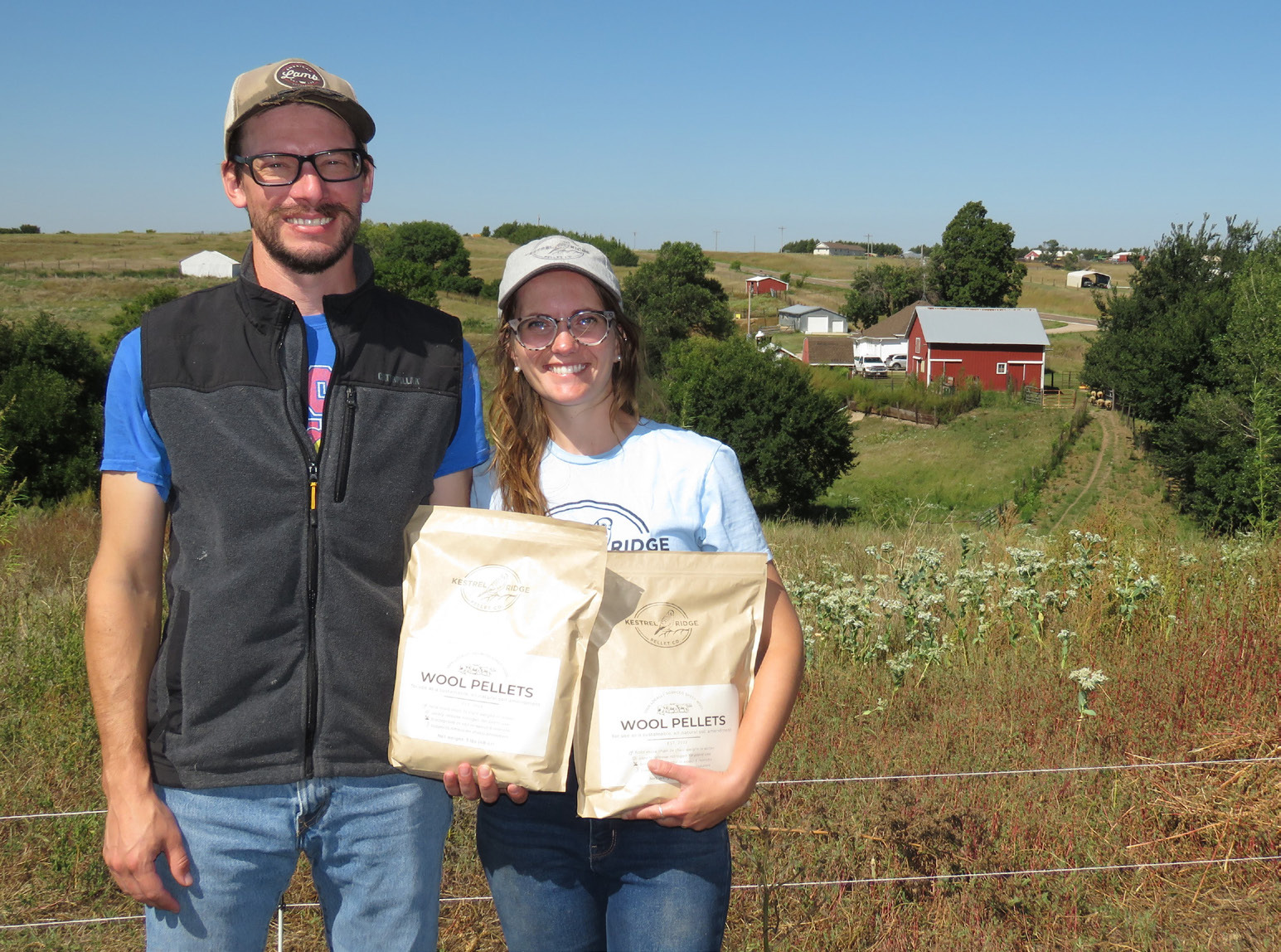
Megan Landes-Murphy and her husband Tom Murphy fulfilled a dream in 2021 when they bought some sheep and 12 acres of mostly pasture land along Highway 4 near Lawrence. Their 100-year-old house, barn and other outbuildings stand in the background. Lori Potter|for the Flatwater Free Press